Just as a mechanic takes good care of a car’s engine to make sure it is always ready to go and able to deliver maximum performance, we take the same level of care when it comes to optimising processes and process technology. This puts us in the perfect position to offer process and functional improvements so you can create uniform working standards for all your employees. Our experts link these standards in work value maps to map complex work. A work value map consists of several service categories. We use to these categories to identify how much a service costs and how much revenue it generates.
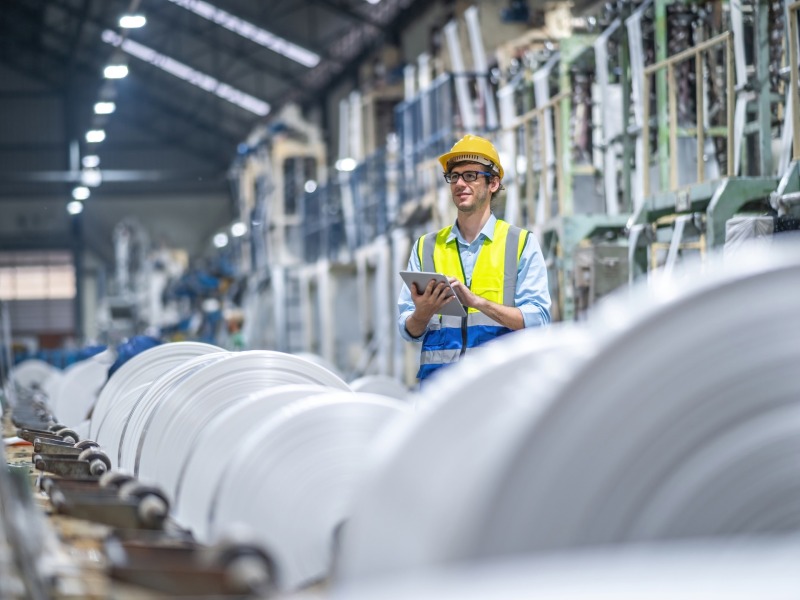
Process optimisation
Our solutions for the process and process engineering industry
New applications for processes and process engineering
Providing standardised processes
Many companies think that their procedures and processes are too individual to be able to compare them with the processes that other companies use. This situation resulted in the creation of the normling. A normling is built and documented digitally – there is no physical version. It is a plant that exists exclusively in the virtual world and could theoretically be located at any plant operator’s site. This means that the normling can be used as the neutral abstraction basis from which processes, functions and systems can be derived. This basis has made it is possible to establish cross-company benchmarks in the market for the first time. It eliminates the discussion of ‘but everything is different in my case’ because we abstract from a neutral object that every operators could use.
The DIN SPEC group 77221 was founded to establish this standard. The committee records its findings and universal descriptions in an official DIN document. The fact that everything is virtual enables every plant operator to carry out an actual comparison.
Our services at a glance:
Our products at a glance:
Our experts are here to support you and your company with regard to process optimisation and improving efficiency. We offer operational support for every product.
-
CALATENA
CALATENA is an application that ensures a continuous data flow between everyone involved in maintenance. You can choose the range of functions you want in the CALATENA app, allowing you to create customised, flexible workflows. The benefits of this include:
- An up-to-date overview of all maintenance tasks is available 24/7.
- Structured data is available for your statistics and business intelligence solutions.
- Coordinating and parallelising tasks ensure an increase in productivity – and the duration of non-productive work is almost halved.
CALATENA represents the processes on the shop floor. The ‘CALATENA goes SAP’ project is the perfect modular addition to SAP 4/Hana. As a perfect symbiosis of SAP to the shop floor, CALATENA leads to all third parties participating in the overall process.
-
ISP
ISP is an interactive tool for maintaining master data, managing documents and monitoring supplier performance. It supports you seamlessly in the preparation of audits, checks, surveys, acceptances and inspections.
ISP offers you full support in the optimisation of all corporate processes and structures. The benefits of this include:
- ISP is modular. That means you are free to combine the individual modules according to what you need and do not have to purchase a large all-in-one package. ISP can be used immediately as standard software and can still be modified according to your needs later.
- ISP can be used interactively.
- ISP is web-based and can therefore be used regardless of location.
The modules of the Interactive Service Portal at a glance:
- ISP Industrial Service Management: This module deals with the topics of standard service specifications, service specifications and administration.
- ISP Accident Management: This module deals with operational accident processing with accident reports, analytics with accident evaluation and accident prevention measures, as well as accident statistics.
- ISP Safety Management: This module deals with operational safety for complying with occupational health and safety laws and risk assessments.
- ISP Data Management: This module deals with master and organisational data management, data optimisation, error prevention and the optimal use of company data.
- ISP Supplier Management: This module deals with deliveries and services. This includes integrated service processing, service definitions, analyses and acceptance, supplier evaluation, ordering, deadline security, cost calculation and quality management.
- ISP Quality Management: This module deals with the quality of company processes using checklists, questionnaires, catalogues of measures and systematically presenting process flows.
- ISP Environmental Management: This module deals with corporate environmental protection, hazard inspections, analyses and measures, checklists and catalogues of measures as well as compliance with environmental regulations and testing standards.
-
LiBu contract management
LiBu is a supplier assessment on a technical level.
LiBu allows you to organise the management of external service providers at one or more locations and ensure your company’s health, safety, environment and quality for occupational accident management.
In addition, LiBu supports you with the acceptance of services, the documentation as well as the administration of the necessary certificates and qualifications of your employees and their attendance times at the locations. This enables you to prevent disruptions in operating process and avoid losses.
With the help of LiBu, our experts collect extensive volumes of data in your company, evaluate the data they obtain and derive suggestions for improvement.
Insights into our daily work
Our testimonials give you an insight into our daily work and the various projects we implement to help manufacturing companies optimise workflows and propose process-related and functional improvements. Our customers include ThyssenKrupp, BP, Deutsche Bahn and Bayer.
Do you have any questions?
There is no website or brochure which can replace a personal meeting to talk about your goals and topics. We are looking forward to an appointment on site.